近年、調達代行というサービスを展開する企業が増えてきています。
サプライヤーの新規開拓、発注先の選定、納期や品質の管理といった調達業務をアウトソーシングする事で、調達部門の限られたリソースを優先度の高い業務に振り向けることができるサービスだそうです。
確かに、労働力が不足している日本でこのようなサービスのニーズが高まっている事は自然な成り行きかもしれませんが、調達代行サービスを展開している企業は大きく2つに区分する事ができるようです。
このコラムでは、その4つの理由について説明していきます。
サプライヤーの新規開拓、発注先の選定、納期や品質の管理といった調達業務をアウトソーシングする事で、調達部門の限られたリソースを優先度の高い業務に振り向けることができるサービスだそうです。
確かに、労働力が不足している日本でこのようなサービスのニーズが高まっている事は自然な成り行きかもしれませんが、調達代行サービスを展開している企業は大きく2つに区分する事ができるようです。
- 自社工場を持たず、実際にモノづくりをしていない企業(以下、商社)
- 自社工場を持ち、実際にモノづくりをしている企業(以下、メーカー)
このコラムでは、その4つの理由について説明していきます。
①コストダウンする事ができる
一般には、商流が深くなるほど仲介する企業が増え、その分手数料や輸送費などがかさんでコストが増加しますので、単純に個々の企業の価格競争力だけを見ていては、結果としてコストダウンに繋がらないことがあります。
つまり、商流が浅くなるようにサプライチェーンを構築する事でコストダウンに繋げることができます。
ここで、商社とメーカーにそれぞれ調達代行を委託した場合の商流とコストを見ていきましょう
つまり、商流が浅くなるようにサプライチェーンを構築する事でコストダウンに繋げることができます。
ここで、商社とメーカーにそれぞれ調達代行を委託した場合の商流とコストを見ていきましょう
商社に調達代行を委託する場合の一般的な商流
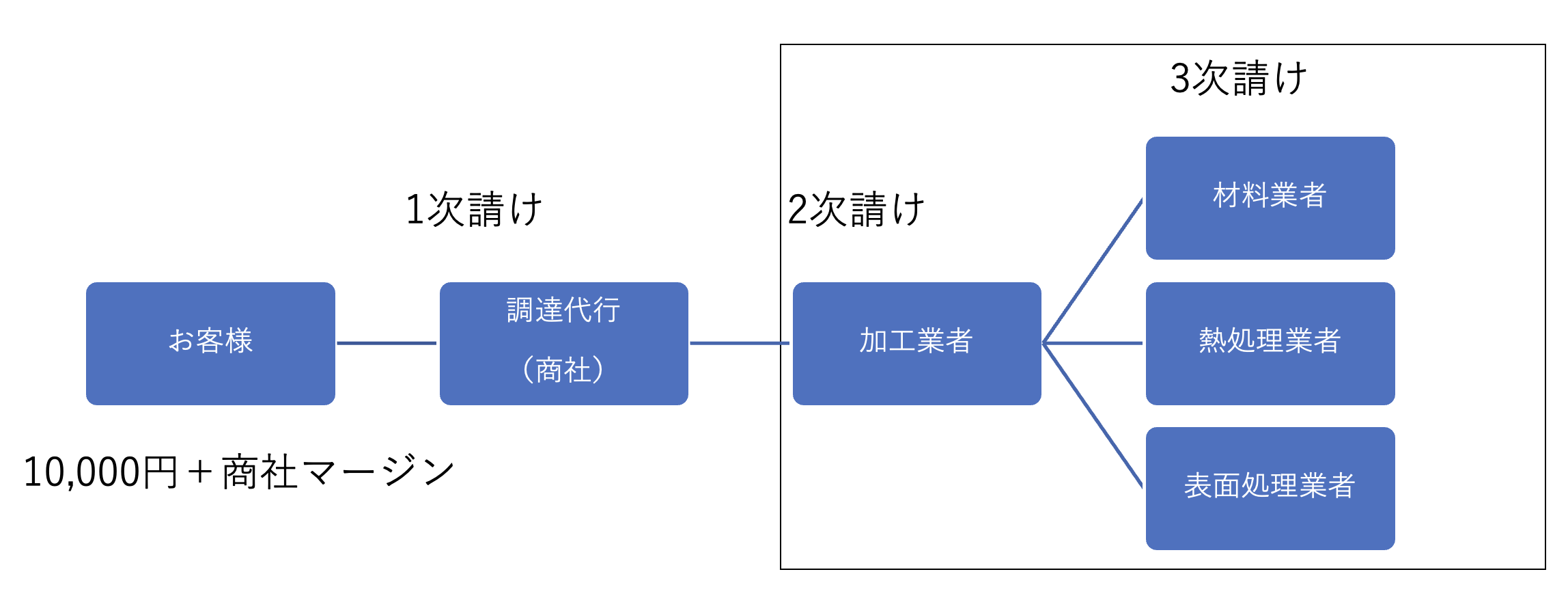
商社は自社工場を持っいないため、モノづくりができる2次請け企業に製造を委託します。
そして、機械加工部品は材料、機械加工、熱処理、表面処理など多くの工程を経て完成品となる訳ですが、一般にはそれぞれ別の企業がその工程を担っているケースが多く、それらの工程を取りまとめる2次請け企業が、さらにその先の3次請け企業と連携してモノづくりを行います。
次に3次請けまで商流が深くなった場合のコストを見てみましょう。
仮に、2次請けが全工程を取りまとめて10,000円で機械加工部品を作り、1次請けの商社に納品したとしましょう。
商社はお客様に調達代行という付加価値を提供している訳ですので、そのマージン分を上乗せした価格がお客様の調達価格になります。
その商社マージンが何%かは取引条件により大きく異なりますが、あらかじめ製品の価格や仕様が決まっていて流通在庫から短納期で入手できる規格品やカタログ品と違い、機械加工部品は言わば「お客様の個別要求に合わせて作る特注品」のような扱いになりますので、その分品質や納期の管理工数が増え、通常より高いマージンを設定する事が考えられます。
そして、機械加工部品は材料、機械加工、熱処理、表面処理など多くの工程を経て完成品となる訳ですが、一般にはそれぞれ別の企業がその工程を担っているケースが多く、それらの工程を取りまとめる2次請け企業が、さらにその先の3次請け企業と連携してモノづくりを行います。
次に3次請けまで商流が深くなった場合のコストを見てみましょう。
仮に、2次請けが全工程を取りまとめて10,000円で機械加工部品を作り、1次請けの商社に納品したとしましょう。
商社はお客様に調達代行という付加価値を提供している訳ですので、そのマージン分を上乗せした価格がお客様の調達価格になります。
その商社マージンが何%かは取引条件により大きく異なりますが、あらかじめ製品の価格や仕様が決まっていて流通在庫から短納期で入手できる規格品やカタログ品と違い、機械加工部品は言わば「お客様の個別要求に合わせて作る特注品」のような扱いになりますので、その分品質や納期の管理工数が増え、通常より高いマージンを設定する事が考えられます。
メーカーに調達代行を委託する場合の一般的な商流
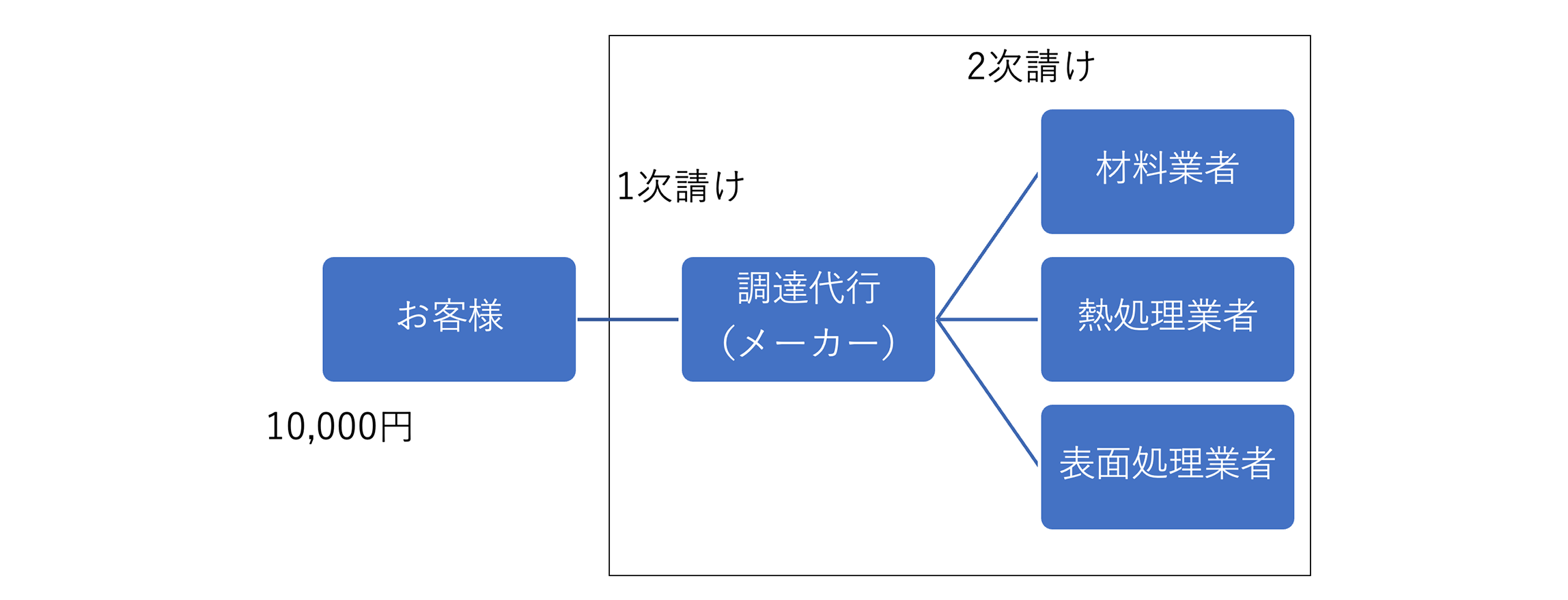
一方、実際にモノづくりができるメーカーが1次請けになると商流は2次請けにまで浅くする事ができ、その結果として、商社マージンが無くなり10,000円で製品を調達する事が可能となります。
さらに、直接取引をする事で各種確認や問合せなどにかかる労力(コミュニケーションコスト)や、サプライチェーンのリスク管理が容易になる事で、金額には表れない間接的なコストを削減する事も可能です。
さらに、直接取引をする事で各種確認や問合せなどにかかる労力(コミュニケーションコスト)や、サプライチェーンのリスク管理が容易になる事で、金額には表れない間接的なコストを削減する事も可能です。
②直接、技術・品質・価格・納期等のコミュニケーションが取れる
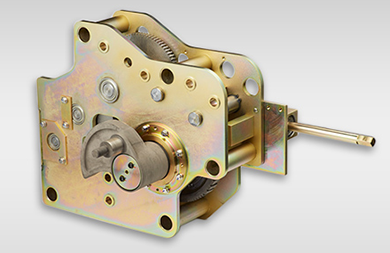
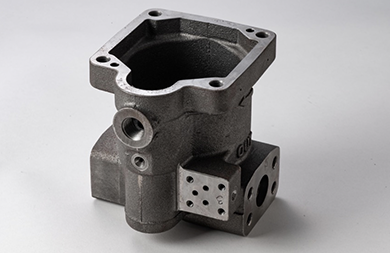
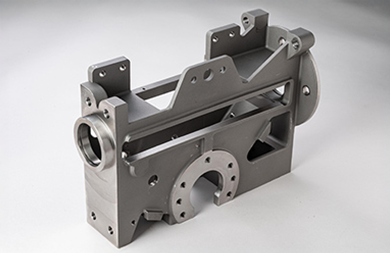
最適なサプライヤーを選定した上で、間違いの無い図面や仕様書などの製造に必要な情報を注文書と共に全て用意できれいれば、お客様とサプライヤーとの間でそれ以上のコミュニケーションは必要ありませんが、そのようなケースは少ないかもしれません。
実際には注文書を頂いたのちに、お客様と様々なコミュニケーションを取らせて頂く機会が多くあります。
このような、加工を行う上で明確にしておきたい情報の確認が遅れると、その分加工の着手が遅れ、ひいては納期の遅延にも繋がりかねないので、できるだけ早期にクリアにしておく必要があります。
その点、モノづくり企業と直接コミュニケーションを取れることで納期遅延リスクを最小化する事ができます。
また、我々の経験上、そのようなコミュニケーションから普段知りえない情報をお聞きする事で新たなご提案(VA/VEなど)をする事ができたというケースが多くあります。
実は設計をされているお客様も「本当にこれで良いのだろうか・・」と迷いながら図面を描いている方も多いようで、中には我々に相談して頂いた後に製図に取りかかるお客様もいらっしゃいます。
モノづくりについての知識や経験が乏しい商社に調達代行を委託してしまうと、このような有益なご提案をする機会が減ってしまう懸念があります。
また、お客様とメーカーが行うコミュニケーションの伝達者としての役割しか果たせないばかりか、迅速なコミュニケーションの妨げとなり、問題解決や意思決定の遅れが納期にも影響を及ぼす可能性すらあります。
ここ最近の傾向として、特に「鋳物製品」の調達に苦労されているお客様が多くいらっしゃる様です。
鋳物の様な、特殊形状をした材料を用いての機械加工は「位置出しの難しさ」から難易度が非常に高く、さらに、材料起因の「鋳巣(ちゅうす)」等の問題も大きな悩みの種となります。
こちらに鋳物の代表的な不適合事例が掲載されています。
加えて鋳物を製作するにあたっては、専用の「型」が必要になる場合が多く、初期費用が高額になる為、お客様からの「支給」になる場合が多くあります。
その様なケースでは、技術的なやり取りや試作検証・測定を何度も行った上で、製作に取り掛かることで、材料歩留まりの改善は勿論、加工・品質保証の工程で後戻りを無くし、結果的に高品質・短納期に繋がるケースも多いです。
実際には注文書を頂いたのちに、お客様と様々なコミュニケーションを取らせて頂く機会が多くあります。
- 図面の間違いや解釈についての確認。
- 市場性の無い材料や、加工できない形状の代替提案
- 検査が難しい部位などについての検査方法の確認。
このような、加工を行う上で明確にしておきたい情報の確認が遅れると、その分加工の着手が遅れ、ひいては納期の遅延にも繋がりかねないので、できるだけ早期にクリアにしておく必要があります。
その点、モノづくり企業と直接コミュニケーションを取れることで納期遅延リスクを最小化する事ができます。
また、我々の経験上、そのようなコミュニケーションから普段知りえない情報をお聞きする事で新たなご提案(VA/VEなど)をする事ができたというケースが多くあります。
実は設計をされているお客様も「本当にこれで良いのだろうか・・」と迷いながら図面を描いている方も多いようで、中には我々に相談して頂いた後に製図に取りかかるお客様もいらっしゃいます。
モノづくりについての知識や経験が乏しい商社に調達代行を委託してしまうと、このような有益なご提案をする機会が減ってしまう懸念があります。
また、お客様とメーカーが行うコミュニケーションの伝達者としての役割しか果たせないばかりか、迅速なコミュニケーションの妨げとなり、問題解決や意思決定の遅れが納期にも影響を及ぼす可能性すらあります。
ここ最近の傾向として、特に「鋳物製品」の調達に苦労されているお客様が多くいらっしゃる様です。
鋳物の様な、特殊形状をした材料を用いての機械加工は「位置出しの難しさ」から難易度が非常に高く、さらに、材料起因の「鋳巣(ちゅうす)」等の問題も大きな悩みの種となります。
こちらに鋳物の代表的な不適合事例が掲載されています。
加えて鋳物を製作するにあたっては、専用の「型」が必要になる場合が多く、初期費用が高額になる為、お客様からの「支給」になる場合が多くあります。
その様なケースでは、技術的なやり取りや試作検証・測定を何度も行った上で、製作に取り掛かることで、材料歩留まりの改善は勿論、加工・品質保証の工程で後戻りを無くし、結果的に高品質・短納期に繋がるケースも多いです。
③実際にメーカーの工場を監査できる
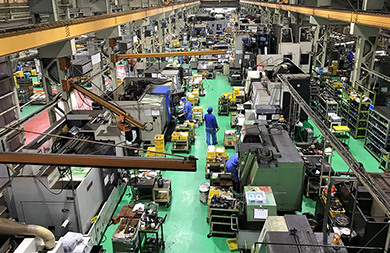
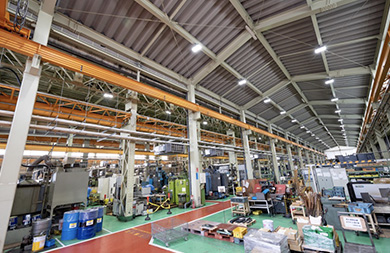
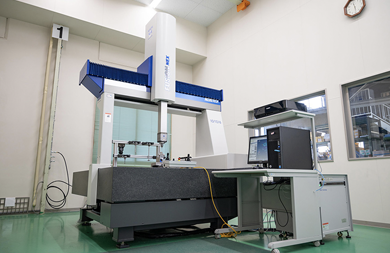
一般に、モノづくりを行っている企業では工場監査が広く行われています。
自社の工場を内部の人員で行う監査(第一者監査)、お客様が行う監査(第二者監査)、ISOなどの認証機関が行う監査(第三者監査)、というように様々な立場の方が工場監査に携わりますが、その目的はどれも同じく、以下の確認を行う事です。
お客様の監査については1~2回/年くらいの頻度で受審していますが、最近は実地で行わず書類だけで済ませる簡易的な監査が増えてきています。
一方で、モノづくりの業界ではお客様は自社で設計した部品をサプライヤーから調達し、自社で組立・検査をしてエンドユーザー様に製品を納入するという分業が一般的になっている中で、部品がどのように作られているのかを知らないお客様も少なくないように思います。
当社では、監査に来て頂ければ工場もご案内しますし、製造についての詳細な説明もさせて頂いております。
1度で全てを知る事はできないにしても、実際に自分の目で見た事があるという経験があるのと無いのとでは大きな違いがあるのではないかと思います。
豊富な一貫生産体制の実績がある当社の場合は、鋳物(材料)・熱処理・表面処理等の各メーカー様と既に十分な実績を積んでいることから、工場見学・監査などにも積極的に対応頂けますし、小ロットでの試作対応もスピーディーに検討することが可能です。
また、当社と各専門メーカーが直接現場で打ち合わせを行うことで、製造工程・加工順番を柔軟に調整し、思わぬリスクの回避や、工程の改善に伴う納期短縮などの副次的なメリットが生まれることもあります。
ここで商社に調達代行を委託した場合について考えてみましょう。
一般に、商社はいわゆる「商社外し」を警戒してサプライヤーの情報を開示することに消極的です。
そのような状況で、お客様が2次サプライヤーとなるメーカーの監査を行うのは難しいと考えられます。
また、モノづくりの知見と監査のノウハウを持ち合わせている商社は皆無ですので商社自らサプライヤーの監査を実施することは考えにくく、実施したとしても形式的なものにとどまり、有意義な監査になる可能性が低いと思われます。
自社の工場を内部の人員で行う監査(第一者監査)、お客様が行う監査(第二者監査)、ISOなどの認証機関が行う監査(第三者監査)、というように様々な立場の方が工場監査に携わりますが、その目的はどれも同じく、以下の確認を行う事です。
- 品質マネジメントシステムが適切に機能しているか
- お客様の要求事項や適用される法令規制に適合したモノづくりが行われているか
- 継続的改善や不適合の再発防止がきちんと行われているか。
お客様の監査については1~2回/年くらいの頻度で受審していますが、最近は実地で行わず書類だけで済ませる簡易的な監査が増えてきています。
一方で、モノづくりの業界ではお客様は自社で設計した部品をサプライヤーから調達し、自社で組立・検査をしてエンドユーザー様に製品を納入するという分業が一般的になっている中で、部品がどのように作られているのかを知らないお客様も少なくないように思います。
当社では、監査に来て頂ければ工場もご案内しますし、製造についての詳細な説明もさせて頂いております。
1度で全てを知る事はできないにしても、実際に自分の目で見た事があるという経験があるのと無いのとでは大きな違いがあるのではないかと思います。
豊富な一貫生産体制の実績がある当社の場合は、鋳物(材料)・熱処理・表面処理等の各メーカー様と既に十分な実績を積んでいることから、工場見学・監査などにも積極的に対応頂けますし、小ロットでの試作対応もスピーディーに検討することが可能です。
また、当社と各専門メーカーが直接現場で打ち合わせを行うことで、製造工程・加工順番を柔軟に調整し、思わぬリスクの回避や、工程の改善に伴う納期短縮などの副次的なメリットが生まれることもあります。
ここで商社に調達代行を委託した場合について考えてみましょう。
一般に、商社はいわゆる「商社外し」を警戒してサプライヤーの情報を開示することに消極的です。
そのような状況で、お客様が2次サプライヤーとなるメーカーの監査を行うのは難しいと考えられます。
また、モノづくりの知見と監査のノウハウを持ち合わせている商社は皆無ですので商社自らサプライヤーの監査を実施することは考えにくく、実施したとしても形式的なものにとどまり、有意義な監査になる可能性が低いと思われます。
④将来的にサプライヤーから真のパートナーとなる可能性がある
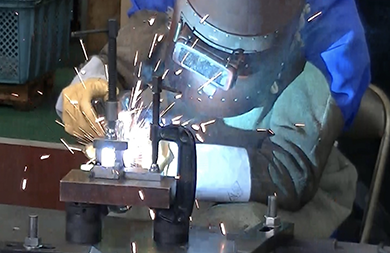
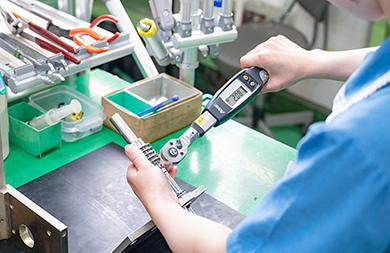
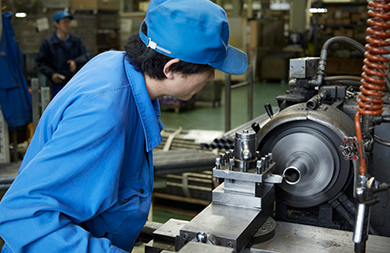
お客様が新規にサプライヤーを探す一番大きな理由は、
現状抱えている課題が既存のサプライヤーだけでは解決できないからだと思います。
当社も年に数社ほど新規のお客様とお取引をさせて頂いていますが、どのお客様も例外なく課題を抱えておりますが、その課題は各社様々といった状況です。
そんな状況の中で重要になってくる考え方としては、「それらの課題に対する提案力を持ったサプライヤーと長期的な視点で取引を行う」事ではないでしょうか。
当初は個別の課題を解決する事が目的で取引を開始したお客様も、取引を重ねる中でサプライヤーの品質、納期対応力、技術力や会社の雰囲気といった深いところまで見えるようになると、別の課題に対する提案を期待して、様々なお声をかけて頂けるようになります。
提案力のあるサプライヤーは、お客様のそれらの課題に対して1つ1つ提案を積み重ねていく事で信頼関係を築き、将来的にサプライヤーから真のパートナーとなっていきます。
実際に当社でも、最初は数件だったお取引が3年ほどかけて5倍、10倍になった事例があります。
現状抱えている課題が既存のサプライヤーだけでは解決できないからだと思います。
当社も年に数社ほど新規のお客様とお取引をさせて頂いていますが、どのお客様も例外なく課題を抱えておりますが、その課題は各社様々といった状況です。
- 既存のサプライヤーが廃業した(廃業しそうだ)。
- 既存のサプライヤーで品質や納期の問題が解消されない。
- 製品の増産を検討しているが既存のサプライヤーにはそれを取り込める余剰生産能力が無い。
- 技術的に難易度が高くて既存のサプライヤーでは対応できない。
そんな状況の中で重要になってくる考え方としては、「それらの課題に対する提案力を持ったサプライヤーと長期的な視点で取引を行う」事ではないでしょうか。
当初は個別の課題を解決する事が目的で取引を開始したお客様も、取引を重ねる中でサプライヤーの品質、納期対応力、技術力や会社の雰囲気といった深いところまで見えるようになると、別の課題に対する提案を期待して、様々なお声をかけて頂けるようになります。
提案力のあるサプライヤーは、お客様のそれらの課題に対して1つ1つ提案を積み重ねていく事で信頼関係を築き、将来的にサプライヤーから真のパートナーとなっていきます。
実際に当社でも、最初は数件だったお取引が3年ほどかけて5倍、10倍になった事例があります。
まとめ
このコラムでは、当社が機械加工部品(切削加工、溶接加工、板金加工など)の調達において
実際にモノづくりをしている企業(メーカー)との直接取引をお勧めする理由について解説してきました。
ポイントは、調達したい製品によりサプライヤーの得手不得手が異なるので、それをよく見極める事かと思います。
当社は、ものづくりの街である燕三条地域に隣接した地の利を最大限に活かし
自社で対応できない工程も協力会社と連携することで、お客様にご満足頂ける一貫生産体制を構築してまいりました。
当社に調達代行をご依頼頂ければ、お客様の調達に係わる煩雑な業務を削減することが可能です。
当社の一貫生産体制のメリット・工数削減事例についてはこちらをご覧ください。
御社の調達課題解決のため、一括で業務依頼できるサプライヤーをお探しでしたら渡邊製作所にご相談ください。
実際にモノづくりをしている企業(メーカー)との直接取引をお勧めする理由について解説してきました。
ポイントは、調達したい製品によりサプライヤーの得手不得手が異なるので、それをよく見極める事かと思います。
当社は、ものづくりの街である燕三条地域に隣接した地の利を最大限に活かし
自社で対応できない工程も協力会社と連携することで、お客様にご満足頂ける一貫生産体制を構築してまいりました。
当社に調達代行をご依頼頂ければ、お客様の調達に係わる煩雑な業務を削減することが可能です。
当社の一貫生産体制のメリット・工数削減事例についてはこちらをご覧ください。
御社の調達課題解決のため、一括で業務依頼できるサプライヤーをお探しでしたら渡邊製作所にご相談ください。